Fillet Weld Design Approaches: Maximizing Joint Performance and Visual Appeal for Structural Honesty
In the realm of structural design and manufacture, the relevance of fillet weld style techniques can not be overemphasized. By diligently taking into consideration elements such as weld profile optimization, product choice, joint prep work methods, welding process performance, and visual improvement producers, approaches and engineers can attain an unified balance in between performance and appearance in their bonded frameworks.
Weld Profile Optimization
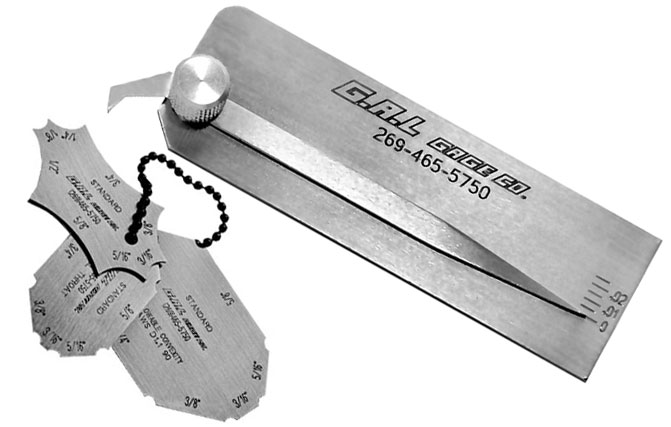

Accomplishing an optimal weld account includes a precise consideration of variables such as product thickness, joint arrangement, welding placement, and preferred welding speed. In addition, the choice of appropriate welding criteria, such as voltage, present, and travel speed, is basic in managing the shape and measurements of the fillet weld. Using advanced welding methods, such as pulse welding or robotic welding, can better fine-tune the weld account to satisfy specific layout demands and quality criteria.
Basically, weld profile optimization is a basic aspect of fillet weld design that directly affects the general efficiency and reliability of bonded joints in structural applications.
Product Selection Factors To Consider
When thinking about product selection for fillet weld style, the compatibility of the base metals is an essential element affecting the structural honesty of the joint. It is important to select products that not only bonded together effectively however additionally possess comparable mechanical buildings to make certain the tons is equally distributed in between the weld and the base steels. Welding materials with significantly different properties can bring about problems such as stress focus, premature joint failing, or breaking.
In addition, the atmosphere in which the welded framework will run have to be taken into consideration when selecting products. Factors like deterioration resistance, temperature fluctuations, and exposure to chemicals can all impact the durability and efficiency of the weld joint. By selecting materials that are suitable for the designated application and atmosphere, the general durability and reliability of the welded joint can be substantially boosted.
As a result, comprehensive factor to consider of material compatibility and environmental aspects is extremely important in making sure the weld joint's toughness, durability, and overall architectural honesty.

Joint Prep Work Strategies
Considering the essential role material selection plays in making sure the architectural honesty of fillet weld joints, it is important to carry out exact joint prep work techniques that optimize the connection between the base metals. Joint preparation is a critical action that straight affects the high quality and stamina of the weld.
In addition, proper fit-up of the joint is vital to make sure consistent circulation of the welding product and protect against defects like incomplete infiltration or excessive buildup. Beveling the edges of the base metals can create a groove that enables much deeper weld infiltration and a more powerful bond. In addition, tack welding the parts in place prior to the last weld assists preserve positioning and reduces distortion during the welding process. By meticulously following these joint preparation techniques, welders can boost the overall performance and appearances of fillet weld joints while ensuring structural soundness.
Welding Process Efficiency
Efficient welding procedures are vital for attaining optimal efficiency and top quality in fillet weld fabrication. Processes like gas steel arc welding (GMAW) and flux-cored arc welding (FCAW) are generally used for fillet welds due to their adaptability and rate.
Routine calibration of welding makers, assessment of consumables, click over here now and maintenance of welding lanterns can protect against downtime and revamp, inevitably conserving time and sources. Well-trained welders are much more adept at adjusting parameters, troubleshooting problems, and preserving consistent weld quality.
Visual Improvement Techniques
To optimize the high quality of fillet weld construction, applying visual enhancement methods can play a crucial role Continued in making sure accuracy and precision during the welding process. Visual aids such as weld size evaluates and amplifying lenses can help in examining weld accounts and measurements precisely. By incorporating these aesthetic improvement approaches right into the welding procedure, welders can attain not just structurally audio fillet welds yet additionally aesthetically enticing outcomes that fulfill sector criteria.
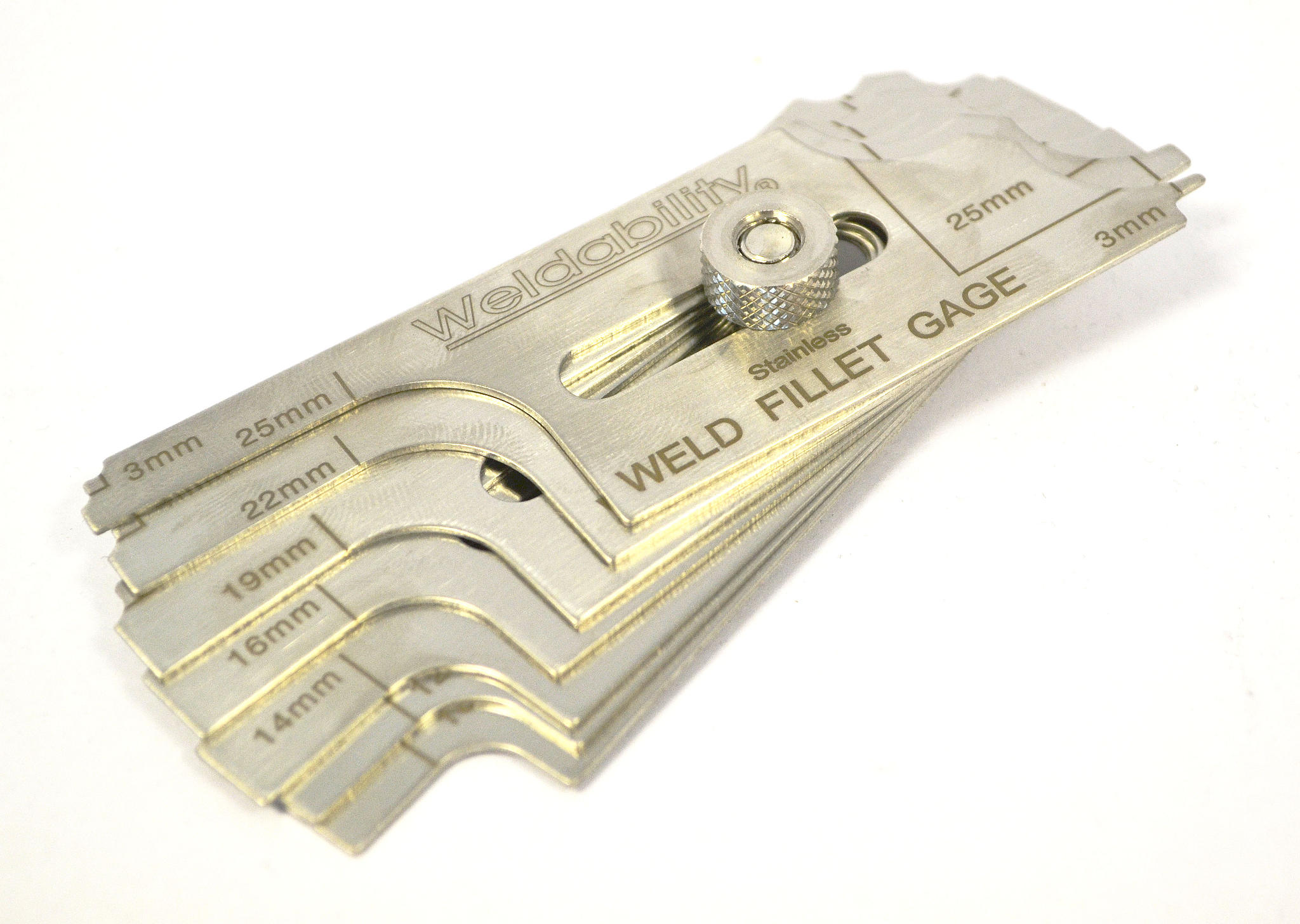
Final Thought
In conclusion, enhancing fillet weld design includes mindful consideration of weld account, material selection, joint prep work, welding process effectiveness, and aesthetic enhancement approaches. By carrying out these strategies, structural honesty can be enhanced while additionally achieving visual appeal. It is necessary to prioritize both efficiency and aesthetics in fillet weld layout to guarantee the total high quality and durability of the joint.
By carefully thinking about variables such as weld account optimization, product selection, joint preparation techniques, welding process efficiency, and visual enhancement producers, techniques and engineers can achieve a harmonious balance in between capability and look in their bonded frameworks.In the world of fillet weld style, enhancing the weld profile plays a vital function in guaranteeing structural click this link integrity and efficiency. The weld account, which consists of the size and shape of the weld cross-section, directly influences the circulation of anxiety and load-bearing capability within the joint. It is necessary to select materials that not just weld together efficiently but also have comparable mechanical buildings to make sure the tons is evenly dispersed between the weld and the base metals - Gauge Fillet Weld.In verdict, enhancing fillet weld design entails cautious consideration of weld account, material option, joint prep work, welding process performance, and visual improvement techniques